The Silent Revolution That Nobody Asked For: Type IL Cement and the Crisis in Concrete Finishing
The concrete industry is facing an unprecedented challenge, and it's time we talked about the elephant in the room: Type IL cement and its impact on finishing operations. While the cement industry quietly transitions to this "environmentally friendly" alternative, contractors across the nation are grappling with a material that's fundamentally different from what they've used for decades.
The Forced Transition
The cement industry is undergoing a major transition to lower its carbon footprint, but at what cost? Type IL cement, which contains up to 15% limestone compared to Type I's 5%, has been thrust upon contractors with minimal education or preparation. This isn't just a minor adjustment – it's a complete overhaul of how concrete behaves during finishing operations.
The Critical Timing Challenge
The finishing window with Type IL cement has become increasingly unpredictable. Contractors are reporting significant issues with project delays and unacceptable finishes. Here's why:
- Modified Setting Behavior The greater limestone content significantly impacts set times, creating a less forgiving window for finishing operations. What worked with Type I cement now requires precise timing and enhanced attention to detail.
- Surface Challenges Type IL concrete tends to have a softer, more porous surface, making it more susceptible to damage during finishing operations. This characteristic demands immediate adaptation in finishing techniques, yet contractors were given little guidance on these necessary changes.
The Industry's Failure
The cement industry's communication breakdown is evident. While some contractors have successfully finished concrete slabs with Type IL cement, others have struggled significantly. This disparity points to a critical lack of education and support during the transition.
Real-World Impacts
The consequences of this hasty transition are severe:
- Increased likelihood of surface defects
- Reduced workability
- Decreased bleeding
- Higher water demand
- Less predictable finishing characteristics
- The Admixture Complication
What makes the Type IL finishing crisis even more complex is its interaction with chemical admixtures. While the cement industry claims there's no significant difference in admixture dosage requirements, the reality on the ground tells a different story. The effectiveness window of admixtures has become notably shorter and less predictable with Type IL cement.
Critical Admixture Considerations:
- Reduced Effectiveness Window The interaction between Portland limestone cement and admixtures requires careful dosage adjustments, with many contractors reporting that the traditional timing windows no longer apply. The effectiveness of water reducers and retarders, in particular, shows a shorter duration compared to their use with Type I cement.
- Temperature Sensitivity Ready-mix producers have had to adjust their approach to retarding admixtures, as the temperature sensitivity of Type IL cement creates a narrower window for effective finishing. What worked with Type I cement now requires precise timing and enhanced attention to detail.
- Modified Dosage Requirements While some producers report no adjustments are needed, others have had to tweak proportions to achieve the desired results. This inconsistency creates additional challenges for contractors who work with multiple suppliers.
The Compressed Timeline Effect
The combination of Type IL characteristics and admixture interactions has created what many contractors call a "compressed timeline effect." This means:
- The window between initial set and final set is less forgiving
- Admixture effectiveness peaks more quickly and diminishes faster
- The traditional timing indicators for finishing operations have become less reliable
Contractors are reporting that the sawing window for some Type IL cement concrete slabs has become more critical and less predictable, leading to increased instances of slab blowouts and finishing challenges.
Real-World Adaptation Strategies
Field Testing and Quality Control The unpredictable nature of Type IL cement requires enhanced testing protocols. Contractors must now conduct more frequent field tests to monitor:
- Initial set times
- Surface water appearance
- Bleed water characteristics
- Early strength development
- Surface hardness progression
- surface durability
Environmental Considerations Temperature control has become more critical than ever. The cement's increased sensitivity to ecological conditionsmeans contractors must:
- Monitor ambient and concrete temperatures more closely
- Adjust placement schedules based on weather forecasts
- Implement more rigorous curing protocols
- Consider night pours during hot weather
- Provide additional surface protection during finishing
Mix Design Modifications With Type IL cement's different specific gravity (~3.09 vs 3.15), contractors need to:
- Adjust mix designs accordingly
- Account for slight volume increases
- Modify water-cement ratios
- Re-evaluate supplementary cementitious material proportions
Economic Impact
The Hidden Costs The transition to Type IL cement has introduced several unexpected costs:
- Increased labor due to more frequent testing and monitoring
- Additional equipment for enhanced quality control
- Higher risk of repairs and callbacks
- Extended finishing time requirements
- More sophisticated temperature control measures
Training Requirements The development of new admixtures and testing of different materials has created an urgent need for:
- Updated finishing techniques training
- New quality control procedures
- Modified scheduling protocols
- Enhanced environmental monitoring skills
- Revised troubleshooting procedures
Future Considerations
Industry Evolution As the concrete industry continues to adapt to Type IL cement, several developments are expected:
- New admixture formulations specifically designed for Type IL cement
- Enhanced testing and monitoring equipment
- Updated industry standards and specifications
- Modified finishing tools and techniques
- Improved education and training programs
Research and Development Needs The industry must focus on:
- Understanding long-term performance characteristics
- Developing more reliable timing indicators
- Creating more effective admixture combinations
- Establishing clearer finishing guidelines
- Documenting regional variations in performance
Call to Action
For Contractors:
- Document and share experiences with Type IL cement
- Invest in updated training programs
- Develop new quality control protocols
- Build relationships with technical support resources
- Maintain detailed records of successful approaches
For Manufacturers:
- Provide more comprehensive technical support
- Develop specific guidelines for different climate zones
- Invest in admixture research and development
- Create better educational resources
- Establish clear communication channels for contractor feedback
For Industry Organizations:
- Update specifications and guidelines
- Provide enhanced training resources
- Facilitate information sharing between stakeholders
- Fund research into improved finishing techniques
- Advocate for contractor concerns
Conclusion
The transition to Type IL cement represents one of the most significant changes in concrete finishing operations in recent history. While the environmental benefits are clear, the industry's failure to adequately prepare for this transition has created unnecessary hardships for contractors. The compressed effectiveness window of admixtures, combined with Type IL's unique characteristics, demands a complete reimagining of concrete finishing practices.
Success in this new era requires a combination of enhanced technical knowledge, modified procedures, and improved communication between all stakeholders. Until manufacturers provide better support and more effective solutions, contractors must remain vigilant in their approach to finishing operations, particularly regarding timing and environmental conditions.
The concrete industry stands at a crossroads. The path forward requires not just adaptation to Type IL cement, but a fundamental shift in how we approach concrete finishing. Only through collective effort and shared knowledge can we hope to overcome these challenges and establish new standards for successful concrete finishing in the Type IL era.
The time has come for the industry to acknowledge these challenges openly and work together toward practical solutions. The future of concrete finishing depends on how well we respond to this challenge today.
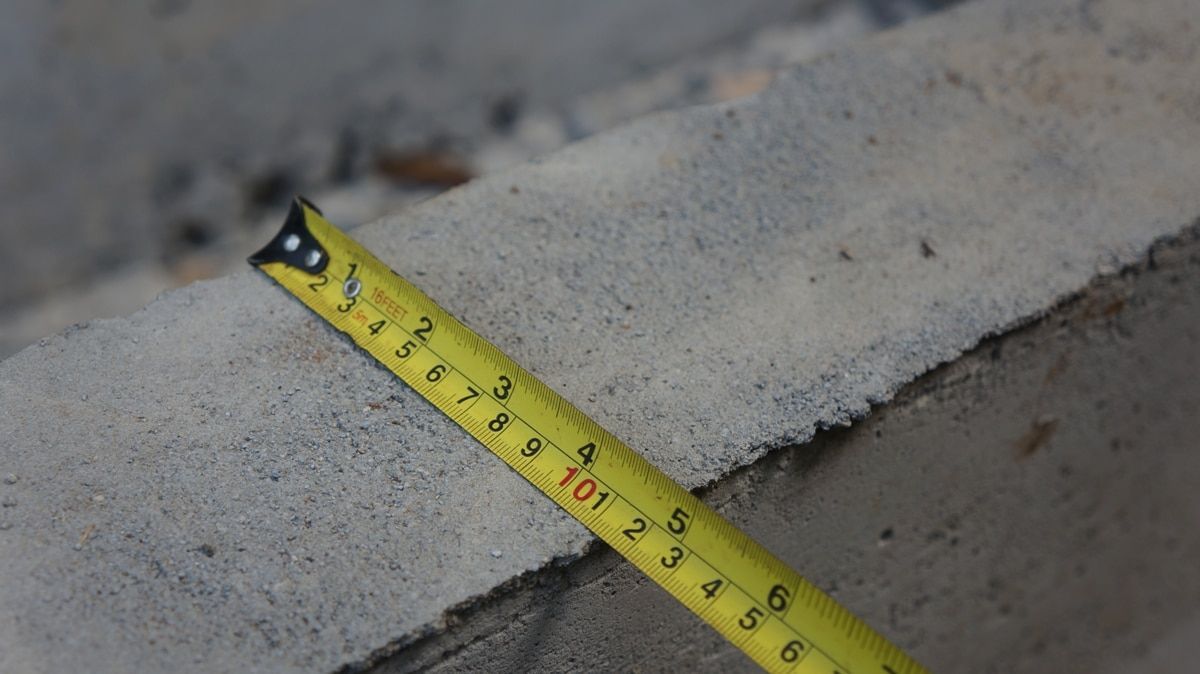
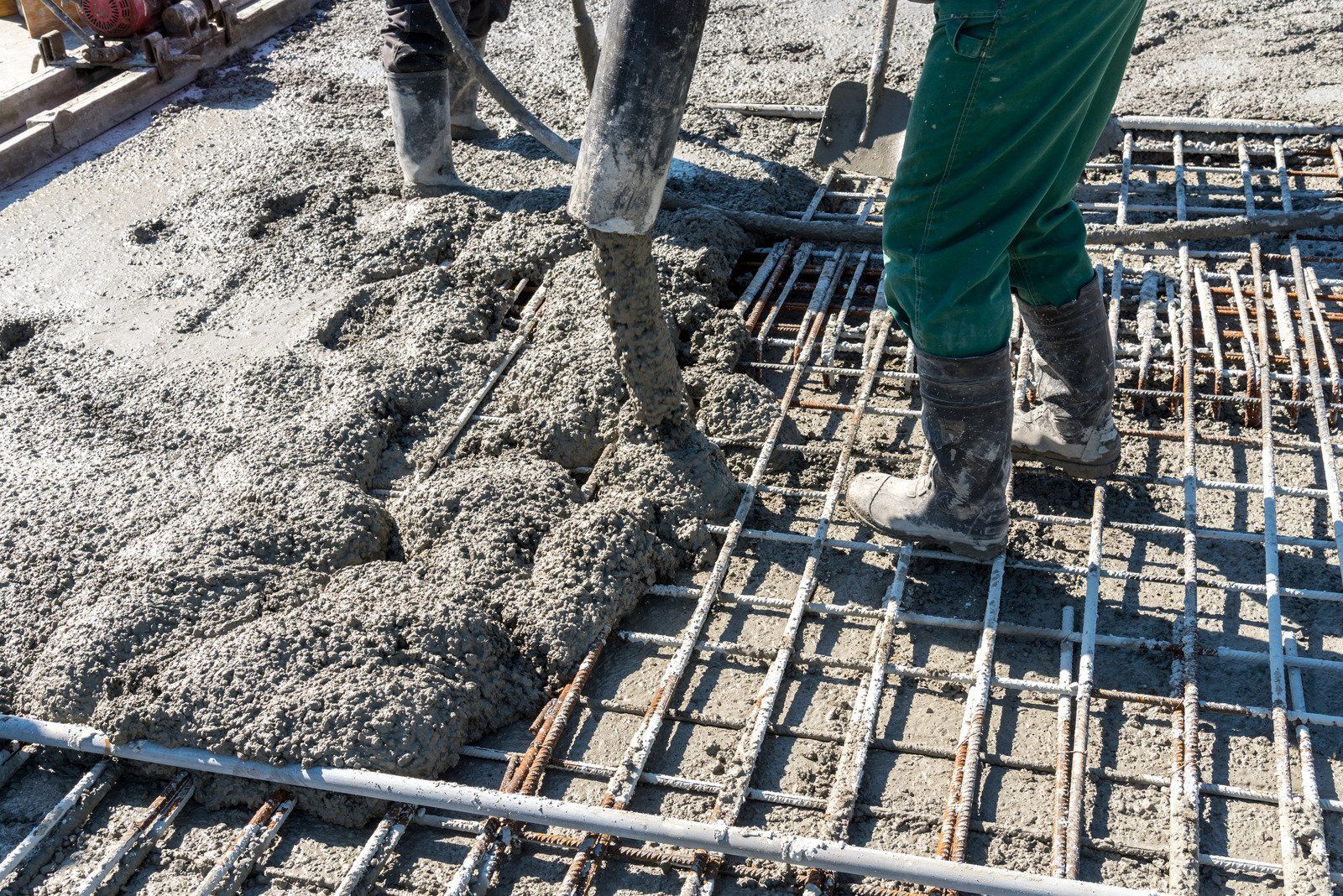
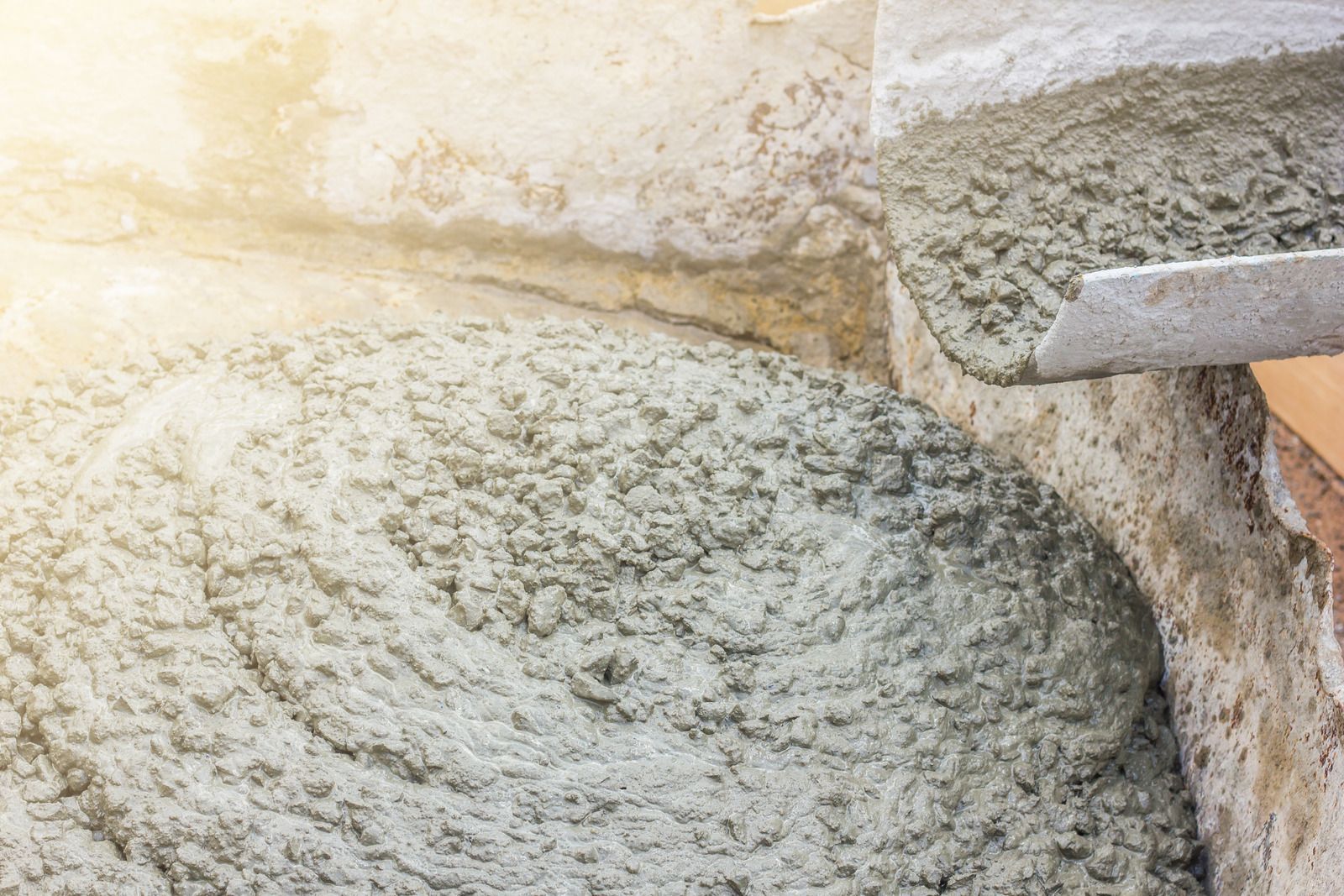